Мокрое торкретирование инъекционным насосом
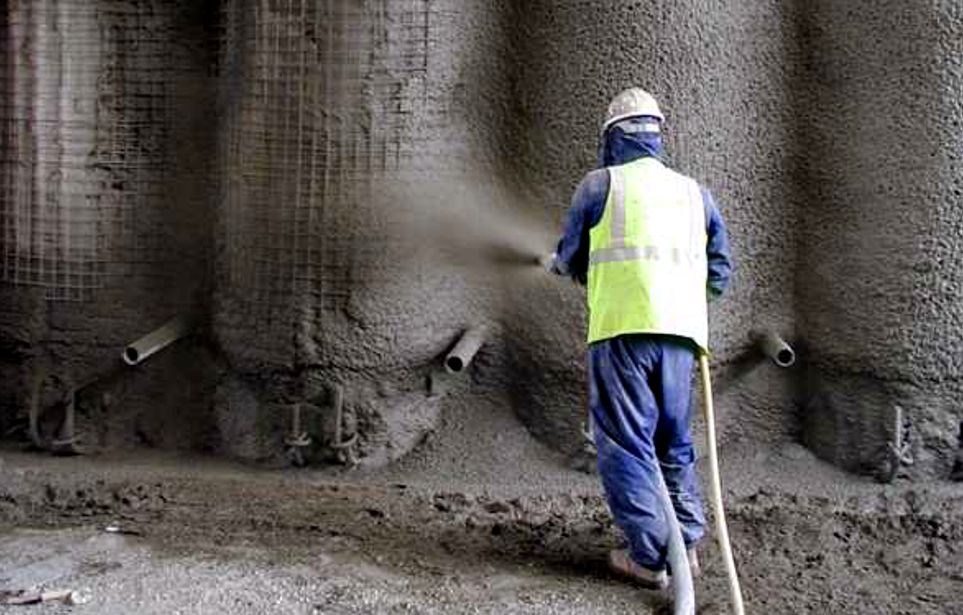
При «мокром» торкретировании смесь цемента, наполнителя, добавок и воды готовится заранее, а затем подаётся в транспортировочный шланг с помощью насоса. Готовый бетонный раствор подается в приемный бункер насоса и перекачивается по трубе или шлангу к торкрет-форсунке. К форсунке также подводится вода для дополнительного увлажнения и сжатый воздух, с помощью которого смесь выбрызгивается.
Бетонный раствор может поставляться в готовом виде с бетоносмесительного узла в автобетоносмесителе или самосвале либо замешиваться на месте из заранее подготовленной сухой смеси. Последнее предпочтительно при небольших объёмах работ, например при ремонтных операциях, а также при ведении работ на площадках, куда затруднён проезд крупногабаритного транспорта. Использование гидратирующих добавок позволяет работать с готовой смесью около 72 часов.
При должном операционном контроле и использовании пластификатором может быть достигнуто минимальное соотношение вода/цемент ниже 45%. Обычно при грамотно подобранной смеси и квалифицированном выполнении работ достигается (при окончательном высыхании через 28 дней) механическая прочность от 30 до 60 МПа.
Обычно методом «мокрого» торкретирования получают бетонные слои толщиной до 150 мм. При необходимости получения слоя большей толщины, работы должны вестись в несколько этапов с временными промежутками, позволяющими бетону приобрести заданную конечную твёрдость.
С помощью «мокрого» торкретирования можно как создавать несущие конструкции, так и вести укрепляющую или декоративную обработку поверхностей, хотя особенно мелкий деталей достичь не удаётся. Для осуществления специфических архитектурных и дизайнерских задумок в смесь также могут быть добавлены пигменты.
Оборудование для «мокрого» торкретирования
В установках «мокрого» торкретирования насосы для подачи бетона могут быть как поршневыми, так и шнековыми. С помощью шнекового насоса плотный поток готовой смеси подаётся к форсунке, куда вводится дополнительный высокоскоростной (130—170 м/сек) поток сжатого воздуха, создаваемый внешним компрессором, который служит несущим и направляющим агентом для бетонной смеси.
Машины со шнековыми насосами имеют ограничение по диаметру наполнителя – до 4 мм, а также не отличаются высокой производительностью – до 4м3/час. Обычно используются для выполнения небольших объёмов ремонтных или декоративных работ.
Работы на торкрет-установках с двухпоршневыми гидравлическими насосами должны вести опытные операторы. «Мокрое» торкретирование требует снижения пульсации при перекачке до минимума с целью обеспечения непрерывной подачи смеси в форсунку для её равномерного и однородного распыления. Для этого применяются различные методы повышения степени заполнения подающих поршней насоса, а также сокращения времени переключения шибера. Машины этого типа могут обеспечивать производительность от 4 до 25 м3/час, позволяет добавлять в смеси наполнители с размером частиц до 20 мм и используются для ведения масштабного строительства, например облицовки тоннелей и возведения крупных конструкций.
Существуют также роторные машины, изначально предназначенные для «сухого» торкретирования, которые могут быть использованы и для «мокрого» процесса. Материал подаётся по шлангу к форсунке давлением сжатого воздуха. Такие установки также позволяют использовать наполнители диаметром до 20 мм и достигают производительности 4-15 м3/час.
Установки «мокрого» торкретирования требуют бережного обращения, регулярной очистки, удаления неиспользованной смеси и промывки в конце каждого рабочего дня во избежание отвердения остатков бетона во внутренних частях оборудования. Перед использованием все соединения должны быть тщательно герметизированы, внутренние поверхности смазаны.
Преимуществами «мокрого» торкретирования, кроме высокой производительности, являются низкий отскок и заметно меньшее, по сравнению с «сухим» процессом, пылеобразование, а также возможность использования более дешевым материалов, например пескоцементной смеси, при отсутствии специальных требований к конечному бетонному покрытию или конструкции. Из недостатоков стоит отметить неизбежность потерь материала, так как количество заранее заготовленной смеси всегда рассчитывается «с запасом».